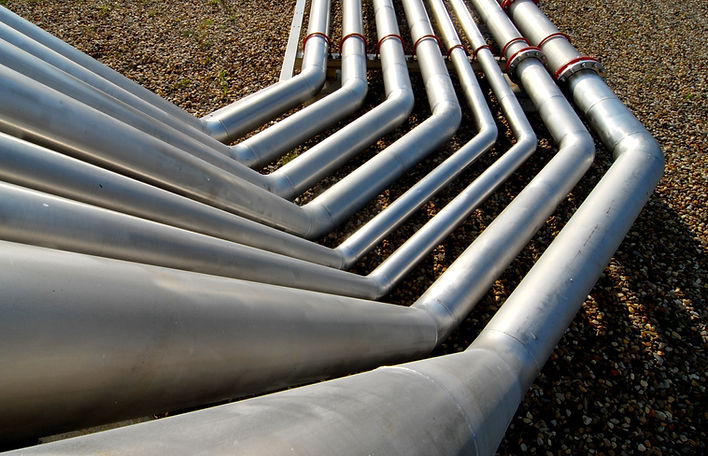
Services & Capabalities
Project Quality Management
Oil & Gas, SMP, Civil Works
Plant, Pipelines, Construction
Auditing, IMS Compliance
Documentation Review
ISO 9001 / 14001 / 45001 / 3834.2 Audit Preparation (pre-audit documentation review & QMS/IMS restructuring). Quality System review / Gap Analysis (business or project specific).
Inspection Test Plan development, Quality & Project Management Plan & Fabrication Methodology creation.
Welding Inspection, Vessels, Piping, Structural
AS 1796 Certificate 10 services.
Vessel / piping / pipeline inspection & compliance (ASME-IX, B31.3, AS 2885)
AS 2214 welding supervision. Structural inspection & compliance (all parts to AS/NZS 1554 series, AS/NZS 5131). Weekly visits or for project duration. Remote / video inspections.
Surveillance, 3rd Party Inspection & Reporting
Surveillance / 3rd party inspection / free issue material inspection. Technical review of contracts, work scope, client specifications, drawings. Technical query assistance (fabrication, welding)
NCR close out / corrective actions advice & management. Kickoff meeting quality assurance representative.
NDT Coordination, Hydrotest Witnessing
Hydrostatic test witnessing/ mechanical testing witnessing at lab for charpy impact & tensile testing.
In house NDT - surface test (before Level II visit) with visual inspection. Thickness & DFT testing. Coordination of NDT for project duration / review of NDT reporting.
Weld Procedure &
Welder Qualification
Weld procedure qualification development / WPS /PQR review (AS/NZS 1554 series / AS 3992, AS 2885, ASME-IX / ASME B31.3).
Welder performance qualification development (ISO9606 / all standards).
Weld repair procedure development & witnessing of repairs.
Flange Management.
FIC & MDR Management
Spool & flange management. Weld, flange & thread mapping & traceability. FIC creation. Verification of NDT %
MDR index creation, review & management. Verification of all deliverables. Walkdowns & punch list handover / management & close out of ITP's (SMP/civil /plant/pipelines)
About Me
Project Quality Management Services (PQMS) was launched to provide project quality management support & assistance for construction projects of a short term duration, mid project intervention, or for project duration, which can cover representation for the kick off meeting attendance & initial quality planning through to progressive ITP sign off, FIC management & then over to client walkdown & MDR handover for onsite as a client-side contractor, direct representative as a part of the PMO team, or as a 3rd party representative.
PQMS can also assist with working towards ISO 9001 compliance for business establishment or assist an existing business to reach readiness for ISO 9001 certification. Identifying the businesses objectives & organisational context to create a business model that mirrors the ISO 9001 requirements as early as possible can save time, money & much heartache!! Creating a lean business model with a structured quality management system extends into & improves both business & project management.
After 20 years working on projects in multiple industries with various business models, PQMS has seen a pattern in the underestimation of conducting sound quality planning & thorough technical reviews, ranging from major projects with renowned companies to minor projects with local businesses, & PQMS endeavours to identify & fill any of the gaps that may be unknowingly missed, the demands of everyday obligations leaves little time to commit to business improvement & can be time consuming & stressful to solve.
PQMS can assist in eliminating any non-conformances & delivering exceptional customer service & product compliance, & achieves this, by creating & implementing effective quality control processes that do not deviate from the ISO 9001 model, this can be incorporated to be project specific utilising the Project Management Body of Knowledge (PMBOK) structure, or business specific under the Integrated Management Systems (IMS) structure.
​
Reviewing & consolidating processes from all departments under the PDCA cycle (Plan, Do, Check, Act) can eliminate nonconformances & improve business operations after a gap analysis of the existing business model has been conducted & a quality focused business improvement strategy has been devised & implemented, no matter how technical the specialty of the business may be.
​
​